Destylacja rozpuszczalników to proces, który polega na oddzieleniu składników mieszaniny na podstawie różnic w ich temperaturach wrzenia. W praktyce oznacza to, że gdy mieszanina jest podgrzewana, składnik o niższej temperaturze wrzenia paruje jako pierwszy, a następnie para jest schładzana i skraplana w osobnym naczyniu. Kluczowym elementem tego procesu jest odpowiednie dobranie sprzętu, który umożliwia efektywne oddzielanie substancji. W laboratoriach chemicznych najczęściej stosuje się destylatory, które mogą mieć różne formy, od prostych kolumn po bardziej zaawansowane urządzenia z frakcjonowaniem. Ważnym aspektem jest także czystość używanych rozpuszczalników oraz ich właściwości fizykochemiczne, które mogą wpływać na efektywność destylacji. Warto również zwrócić uwagę na bezpieczeństwo podczas przeprowadzania tego procesu, ponieważ wiele rozpuszczalników jest łatwopalnych lub toksycznych.
Jakie są zastosowania destylacji rozpuszczalników w przemyśle
Destylacja rozpuszczalników znajduje szerokie zastosowanie w różnych gałęziach przemysłu, w tym w przemyśle chemicznym, farmaceutycznym oraz petrochemicznym. W przemyśle chemicznym proces ten jest wykorzystywany do oczyszczania surowców oraz produkcji wysokiej jakości substancji chemicznych. Na przykład, w produkcji alkoholi etylowych destylacja pozwala na uzyskanie czystego produktu poprzez usunięcie zanieczyszczeń i niepożądanych składników. W przemyśle farmaceutycznym destylacja jest kluczowa dla uzyskania czystych substancji czynnych, które są niezbędne do produkcji leków. Dodatkowo, w branży petrochemicznej destylacja frakcyjna jest stosowana do separacji różnych frakcji ropy naftowej, co pozwala na uzyskanie paliw oraz innych produktów chemicznych.
Jakie są różnice między destylacją a innymi metodami separacji
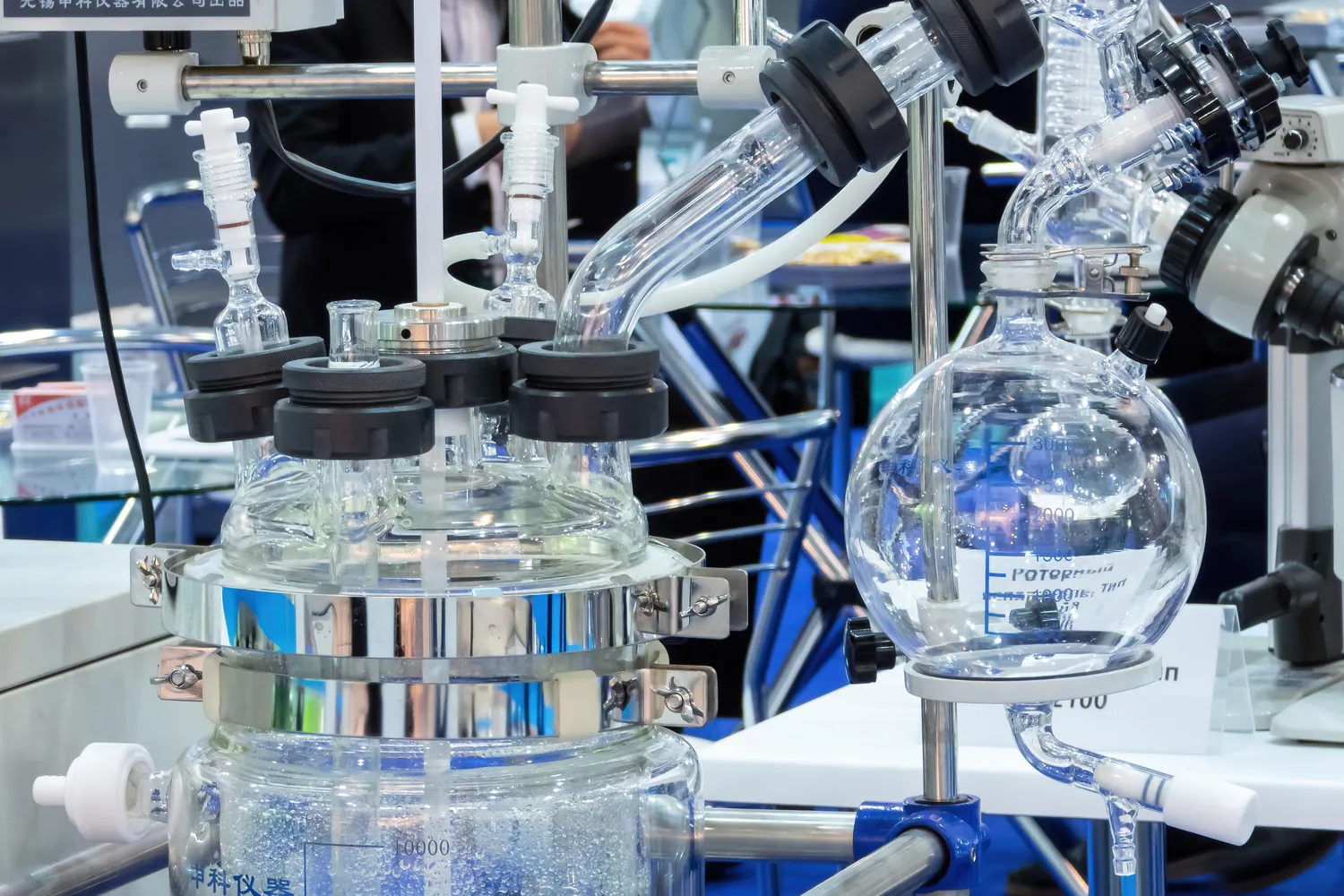
Destylacja rozpuszczalników różni się od innych metod separacji, takich jak filtracja czy ekstrakcja, przede wszystkim zasadą działania oraz zastosowaniem. Filtracja polega na oddzielaniu ciał stałych od cieczy za pomocą materiału filtracyjnego, co sprawia, że jest skuteczna jedynie w przypadku mieszanin zawierających nierozpuszczalne składniki. Ekstrakcja z kolei opiera się na różnicach w rozpuszczalności substancji w różnych rozpuszczalnikach i często wymaga użycia dodatkowych reagentów. Destylacja natomiast bazuje na różnicach temperatur wrzenia i może być stosowana do separacji cieczy od cieczy lub cieczy od gazu. Kolejną istotną różnicą jest to, że destylacja może prowadzić do uzyskania czystych frakcji substancji chemicznych, co jest kluczowe w wielu zastosowaniach przemysłowych i laboratoryjnych.
Jakie są najczęstsze błędy podczas destylacji rozpuszczalników
Podczas przeprowadzania destylacji rozpuszczalników można napotkać wiele pułapek i błędów, które mogą wpłynąć na jakość końcowego produktu oraz bezpieczeństwo procesu. Jednym z najczęstszych błędów jest niewłaściwe ustawienie temperatury grzania, co może prowadzić do niepełnej separacji składników lub ich degradacji. Innym powszechnym problemem jest brak odpowiedniej wentylacji w laboratorium, co zwiększa ryzyko wystąpienia niebezpiecznych oparów lub wybuchów. Ponadto niedostateczna kontrola nad czasem trwania destylacji może prowadzić do utraty cennych składników lub zanieczyszczenia produktu końcowego. Użytkownicy często pomijają także znaczenie kalibracji sprzętu oraz regularnego sprawdzania jego stanu technicznego. Te wszystkie czynniki mogą znacząco wpłynąć na efektywność procesu oraz bezpieczeństwo pracy w laboratorium chemicznym.
Jakie są kluczowe etapy procesu destylacji rozpuszczalników
Proces destylacji rozpuszczalników składa się z kilku kluczowych etapów, które są niezbędne do uzyskania czystego produktu. Pierwszym krokiem jest przygotowanie mieszaniny, która ma być poddana destylacji. Ważne jest, aby składniki były dokładnie wymieszane i miały odpowiednie proporcje, co pozwoli na efektywne oddzielanie ich podczas procesu. Następnie mieszanina jest umieszczana w kolbie destylacyjnej, która jest podgrzewana. W tym momencie zaczyna zachodzić proces parowania – składnik o najniższej temperaturze wrzenia odparowuje jako pierwszy. Para przemieszcza się następnie do chłodnicy, gdzie zostaje schłodzona i skroplona. Skroplony płyn zbiera się w osobnym naczyniu, zwanym odbieraczem. Proces ten można powtarzać wielokrotnie, aby uzyskać coraz czystsze frakcje substancji. Ostatnim etapem jest analiza uzyskanych produktów, aby ocenić ich czystość oraz zgodność z wymaganiami jakościowymi.
Jakie są najważniejsze czynniki wpływające na efektywność destylacji
Efektywność destylacji rozpuszczalników zależy od wielu czynników, które mogą znacząco wpłynąć na wyniki procesu. Jednym z najważniejszych elementów jest temperatura grzania, która musi być odpowiednio dostosowana do właściwości chemicznych składników mieszaniny. Zbyt wysoka temperatura może prowadzić do degradacji substancji lub niepożądanych reakcji chemicznych, podczas gdy zbyt niska może skutkować niepełnym odparowaniem składników. Kolejnym istotnym czynnikiem jest ciśnienie atmosferyczne – w przypadku obniżonego ciśnienia temperatura wrzenia substancji również się zmienia, co może być wykorzystane w tzw. destylacji próżniowej. Również rodzaj używanego sprzętu ma znaczenie; nowoczesne destylatory często wyposażone są w kolumny frakcyjne, które umożliwiają bardziej efektywne separowanie składników o zbliżonych temperaturach wrzenia. Oprócz tego ważna jest także jakość używanych rozpuszczalników oraz ich czystość, ponieważ obecność zanieczyszczeń może wpłynąć na wyniki destylacji i jakość końcowego produktu.
Jakie są różnice między destylacją prostą a frakcyjną
Destylacja prosta i frakcyjna to dwa podstawowe typy procesów stosowanych do separacji składników mieszanin cieczy, jednak różnią się one zasadniczo pod względem zastosowania oraz efektywności. Destylacja prosta jest najczęściej stosowana w przypadku mieszanin zawierających substancje o znacznie różnych temperaturach wrzenia. Proces ten polega na jednorazowym podgrzewaniu mieszaniny i skraplaniu pary, co pozwala na uzyskanie jednego frakcji o wyższej czystości. Jest to metoda stosunkowo szybka i łatwa do przeprowadzenia, ale jej ograniczeniem jest to, że nie sprawdza się w przypadku mieszanin o temperaturach wrzenia bliskich sobie. W takich sytuacjach lepszym rozwiązaniem jest destylacja frakcyjna, która wykorzystuje kolumny frakcyjne do wielokrotnego skraplania i odparowywania składników. Dzięki temu możliwe jest uzyskanie wyższej czystości poszczególnych frakcji oraz skuteczniejsze oddzielanie substancji o podobnych temperaturach wrzenia.
Jakie są najczęstsze materiały wykorzystywane w destylacji
W procesie destylacji rozpuszczalników wykorzystywane są różnorodne materiały, które mają kluczowe znaczenie dla efektywności oraz bezpieczeństwa całego procesu. Najczęściej używanym materiałem do budowy sprzętu destylacyjnego jest szkło borokrzemowe ze względu na swoją odporność na wysokie temperatury oraz chemikalia. Szkło pozwala również na łatwe monitorowanie przebiegu procesu dzięki przezroczystości materiału. W przypadku bardziej zaawansowanych systemów destylacyjnych często stosuje się również stal nierdzewną lub inne metale odpornych na korozję, szczególnie gdy proces dotyczy agresywnych chemikaliów. Dodatkowo istotnym elementem są uszczelki i połączenia wykonane z materiałów odpornych na działanie wysokich temperatur oraz substancji chemicznych, co zapewnia szczelność układu i minimalizuje ryzyko wycieków. Warto także wspomnieć o materiałach wykorzystywanych w chłodnicach – często są to miedź lub aluminium ze względu na ich doskonałe właściwości przewodzące ciepło.
Jakie są nowoczesne technologie stosowane w destylacji rozpuszczalników
Nowoczesne technologie stosowane w destylacji rozpuszczalników znacząco zwiększają efektywność oraz jakość tego procesu. W ostatnich latach rozwój technologii umożliwił wdrożenie innowacyjnych rozwiązań takich jak destylacja membranowa czy wykorzystanie ultradźwięków do wspomagania separacji składników. Destylacja membranowa polega na wykorzystaniu specjalnych membran selektywnych, które pozwalają na przechodzenie tylko określonych składników mieszanki przy jednoczesnym zatrzymywaniu innych. Taki sposób separacji może być znacznie bardziej efektywny niż tradycyjne metody destylacyjne i pozwala na oszczędność energii oraz czasu. Z kolei ultradźwięki mogą być wykorzystywane do intensyfikacji procesu odparowywania poprzez generowanie mikroskopijnych pęcherzyków powietrza w cieczy, co zwiększa powierzchnię kontaktu między cieczą a parą i przyspiesza proces separacji. Dodatkowo automatyzacja procesów destylacyjnych za pomocą zaawansowanych systemów sterowania pozwala na precyzyjne monitorowanie parametrów pracy urządzeń oraz szybką reakcję na ewentualne odchylenia od normy.
Jakie są wyzwania związane z dużymi skalami produkcji
Przemysłowa skala produkcji związana z destylacją rozpuszczalników stawia przed inżynierami i technikami szereg wyzwań, które muszą zostać skutecznie rozwiązane dla zapewnienia efektywności i bezpieczeństwa procesów produkcyjnych. Jednym z głównych problemów jest zarządzanie dużymi ilościami surowców oraz produktów końcowych, co wymaga odpowiednich systemów logistycznych oraz magazynowych. Ponadto większe skale produkcji wiążą się z koniecznością utrzymania stałych parametrów procesu przez dłuższy czas, co może być trudne ze względu na zmiany właściwości surowców czy warunków otoczenia. Również kontrola jakości staje się bardziej skomplikowana; konieczne jest wdrożenie systemów monitorujących jakość produktów w czasie rzeczywistym oraz regularne przeprowadzanie analiz laboratoryjnych. Dodatkowo większe instalacje wymagają znacznych nakładów inwestycyjnych oraz kosztów eksploatacyjnych związanych z energią czy konserwacją sprzętu.