Budowa maszyn pneumatycznych opiera się na kilku kluczowych elementach, które współpracują ze sobą w celu efektywnego działania systemu. Na początku warto wymienić kompresor, który jest sercem całego układu. Jego zadaniem jest sprężanie powietrza, co pozwala na uzyskanie odpowiedniego ciśnienia niezbędnego do pracy maszyn. Kolejnym istotnym elementem jest zbiornik powietrza, który magazynuje sprężone powietrze i zapewnia jego stały dostęp w momencie, gdy maszyna go potrzebuje. Następnie mamy do czynienia z różnymi zaworami, które kontrolują przepływ powietrza w systemie. Zawory te mogą być ręczne lub automatyczne, a ich odpowiednie działanie jest kluczowe dla precyzyjnej pracy maszyny. Warto również zwrócić uwagę na siłowniki pneumatyczne, które przekształcają energię sprężonego powietrza w ruch mechaniczny. Siłowniki te mogą mieć różne kształty i rozmiary, w zależności od zastosowania maszyny. Ostatnim, ale nie mniej ważnym elementem są przewody pneumatyczne, które łączą wszystkie komponenty systemu i umożliwiają transport sprężonego powietrza do poszczególnych części maszyny.
Jakie są najczęstsze zastosowania maszyn pneumatycznych
Maszyny pneumatyczne znajdują szerokie zastosowanie w różnych branżach przemysłowych, co czyni je niezwykle wszechstronnymi narzędziami. W przemyśle produkcyjnym wykorzystywane są do automatyzacji procesów montażowych oraz pakowania produktów. Dzięki swojej szybkości i precyzji, maszyny te przyczyniają się do zwiększenia wydajności linii produkcyjnych. W sektorze budowlanym maszyny pneumatyczne są używane do obsługi narzędzi takich jak młoty udarowe czy wiertnice, co znacznie ułatwia wykonywanie ciężkich prac budowlanych. W motoryzacji natomiast stosowane są w procesach lakierowania oraz montażu części samochodowych. Kolejnym obszarem zastosowań jest przemysł spożywczy, gdzie maszyny pneumatyczne służą do pakowania żywności oraz transportu materiałów sypkich. W medycynie wykorzystuje się je w urządzeniach wspomagających oddychanie oraz w systemach dostarczania leków.
Jakie są zalety i wady maszyn pneumatycznych
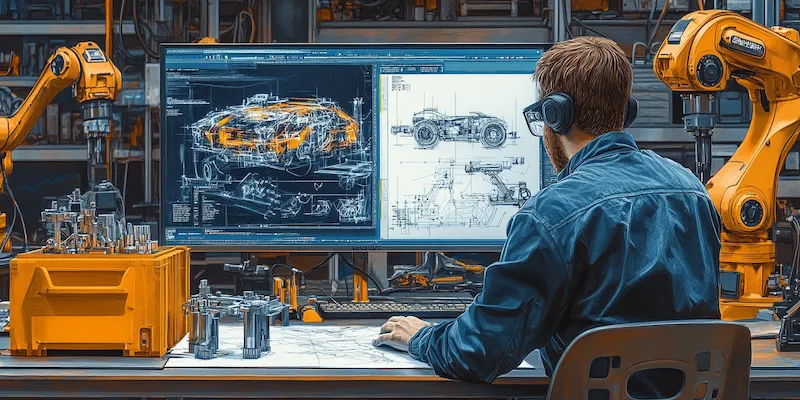
Budowa maszyn pneumatycznych wiąże się z wieloma zaletami, ale także pewnymi wadami, które warto rozważyć przed podjęciem decyzji o ich zastosowaniu. Do głównych zalet należy zaliczyć prostotę konstrukcji oraz łatwość w obsłudze. Maszyny te charakteryzują się niskimi kosztami eksploatacji, ponieważ sprężone powietrze jest powszechnie dostępne i relatywnie tanie w produkcji. Dodatkowo, maszyny pneumatyczne są bardzo szybkie i mogą osiągać wysoką wydajność, co czyni je idealnym rozwiązaniem dla przemysłu wymagającego dużej efektywności. Warto również podkreślić ich bezpieczeństwo – w przypadku awarii nie ma ryzyka wybuchu czy pożaru, co często zdarza się w przypadku maszyn elektrycznych czy hydraulicznych. Z drugiej strony, istnieją także pewne ograniczenia związane z ich użytkowaniem. Maszyny pneumatyczne mogą być mniej wydajne przy pracy na dużych wysokościach ciśnienia oraz wymagają regularnej konserwacji i sprawdzania szczelności układów, aby uniknąć strat energii.
Jakie nowoczesne technologie wpływają na rozwój maszyn pneumatycznych
W ostatnich latach rozwój technologii znacząco wpłynął na budowę maszyn pneumatycznych oraz ich funkcjonalność. Jednym z najważniejszych trendów jest automatyzacja procesów produkcyjnych, która pozwala na zwiększenie wydajności oraz redukcję kosztów operacyjnych. Wprowadzenie systemów sterowania opartych na sztucznej inteligencji umożliwia lepszą kontrolę nad pracą maszyn oraz optymalizację zużycia energii. Dzięki nowoczesnym czujnikom możliwe jest monitorowanie parametrów pracy maszyn w czasie rzeczywistym, co pozwala na szybką reakcję na ewentualne awarie lub nieprawidłowości. Kolejnym istotnym aspektem jest rozwój materiałów wykorzystywanych do produkcji komponentów maszyn pneumatycznych. Nowe materiały charakteryzują się większą odpornością na zużycie oraz korozję, co przekłada się na dłuższą żywotność urządzeń. Również technologie druku 3D zaczynają odgrywać coraz większą rolę w produkcji elementów maszyn pneumatycznych, co pozwala na szybsze prototypowanie oraz dostosowywanie komponentów do indywidualnych potrzeb klientów.
Jakie są kluczowe różnice między maszynami pneumatycznymi a hydraulicznymi
Budowa maszyn pneumatycznych i hydraulicznych różni się zasadniczo w kilku aspektach, co wpływa na ich zastosowanie oraz efektywność w różnych warunkach pracy. Przede wszystkim, maszyny pneumatyczne wykorzystują sprężone powietrze jako medium robocze, podczas gdy maszyny hydrauliczne operują cieczą, najczęściej olejem. Ta fundamentalna różnica ma znaczący wpływ na parametry pracy obu systemów. Maszyny pneumatyczne charakteryzują się mniejszymi rozmiarami i wagą, co czyni je bardziej mobilnymi i łatwiejszymi do zainstalowania w różnych miejscach. Z drugiej strony, maszyny hydrauliczne mogą generować znacznie większe siły, co sprawia, że są bardziej odpowiednie do ciężkich prac przemysłowych, takich jak prasowanie czy formowanie metalu. Kolejnym istotnym czynnikiem jest szybkość działania – maszyny pneumatyczne zazwyczaj działają szybciej niż hydrauliczne, co czyni je idealnymi do zastosowań wymagających dużej dynamiki. Warto również zwrócić uwagę na koszty eksploatacji; sprężone powietrze jest tańsze w produkcji i dostępności niż olej hydrauliczny, jednak systemy pneumatyczne mogą być mniej efektywne energetycznie w dłuższej perspektywie czasowej.
Jakie są najnowsze trendy w projektowaniu maszyn pneumatycznych
W ostatnich latach projektowanie maszyn pneumatycznych uległo znacznym zmianom, które wynikają z postępu technologicznego oraz rosnących wymagań rynku. Jednym z najważniejszych trendów jest miniaturyzacja komponentów, co pozwala na tworzenie bardziej kompaktowych i wydajnych systemów. Dzięki temu maszyny pneumatyczne mogą być stosowane w miejscach o ograniczonej przestrzeni, co zwiększa ich wszechstronność. Również rozwój technologii IoT (Internet of Things) przyczynia się do wzrostu inteligencji maszyn pneumatycznych. Dzięki możliwości zdalnego monitorowania i zarządzania procesami produkcyjnymi, operatorzy mogą optymalizować pracę maszyn oraz szybko reagować na ewentualne problemy. Wprowadzenie zaawansowanych systemów diagnostycznych umożliwia przewidywanie awarii i planowanie konserwacji, co przekłada się na zwiększenie efektywności operacyjnej. Kolejnym istotnym trendem jest ekologiczne podejście do projektowania maszyn pneumatycznych. Producenci coraz częściej stawiają na rozwiązania energooszczędne oraz materiały przyjazne dla środowiska, co wpisuje się w globalne dążenie do zrównoważonego rozwoju.
Jakie są wyzwania związane z eksploatacją maszyn pneumatycznych
Eksploatacja maszyn pneumatycznych wiąże się z szeregiem wyzwań, które mogą wpływać na ich wydajność oraz niezawodność. Jednym z głównych problemów jest utrzymanie odpowiedniego ciśnienia sprężonego powietrza w systemie. Niewłaściwe ciśnienie może prowadzić do nieefektywnej pracy maszyny lub nawet jej uszkodzenia. Dlatego regularne kontrole i konserwacja układów sprężonego powietrza są niezbędne dla zapewnienia prawidłowego funkcjonowania urządzeń. Kolejnym wyzwaniem jest konieczność dbania o szczelność wszystkich połączeń i przewodów, ponieważ nawet niewielkie nieszczelności mogą prowadzić do znacznych strat energii oraz obniżenia wydajności systemu. Warto również pamiętać o wpływie temperatury otoczenia na pracę maszyn pneumatycznych; skrajne warunki mogą negatywnie wpłynąć na ich funkcjonowanie oraz żywotność komponentów. Dodatkowo, operatorzy muszą być odpowiednio przeszkoleni w zakresie obsługi maszyn pneumatycznych, aby uniknąć błędów mogących prowadzić do awarii lub wypadków.
Jakie są przyszłościowe kierunki rozwoju technologii pneumatycznej
Przyszłość technologii pneumatycznej zapowiada się obiecująco dzięki ciągłemu postępowi technologicznemu oraz rosnącym wymaganiom rynku przemysłowego. Jednym z kluczowych kierunków rozwoju jest integracja sztucznej inteligencji w systemach sterowania maszyn pneumatycznych. Dzięki algorytmom uczenia maszynowego możliwe będzie automatyczne dostosowywanie parametrów pracy urządzeń do zmieniających się warunków produkcji oraz optymalizacja procesów w czasie rzeczywistym. Również rozwój technologii bezprzewodowej komunikacji otwiera nowe możliwości w zakresie monitorowania i zarządzania pracą maszyn pneumatycznych zdalnie, co zwiększa komfort użytkowników oraz efektywność operacyjną. Zrównoważony rozwój staje się coraz ważniejszym aspektem projektowania nowych rozwiązań; producenci będą poszukiwać bardziej ekologicznych materiałów oraz metod produkcji, które minimalizują wpływ na środowisko naturalne. Warto również zauważyć rosnącą popularność rozwiązań hybrydowych łączących technologie pneumatyczne z elektrycznymi czy hydraulicznymi, co pozwoli na uzyskanie jeszcze lepszych parametrów pracy oraz elastyczności zastosowań.
Jakie są kluczowe aspekty bezpieczeństwa w pracy z maszynami pneumatycznymi
Bezpieczeństwo w pracy z maszynami pneumatycznymi jest niezwykle istotnym zagadnieniem, które wymaga szczególnej uwagi ze strony zarówno operatorów, jak i pracodawców. Przede wszystkim, każdy pracownik powinien być odpowiednio przeszkolony w zakresie obsługi tych urządzeń oraz znajomości zasad BHP. Ważne jest, aby przed rozpoczęciem pracy przeprowadzać regularne kontrole stanu technicznego maszyn, co pozwala na wczesne wykrycie ewentualnych usterek. Należy również pamiętać o stosowaniu odpowiednich środków ochrony osobistej, takich jak rękawice czy okulary ochronne, które mogą zminimalizować ryzyko urazów. Kolejnym kluczowym aspektem jest zapewnienie właściwej wentylacji w pomieszczeniach, gdzie znajdują się maszyny pneumatyczne, aby uniknąć gromadzenia się sprężonego powietrza oraz innych potencjalnie niebezpiecznych substancji. Warto także wdrożyć procedury awaryjne na wypadek niespodziewanych sytuacji, takich jak wyciek sprężonego powietrza czy awaria maszyny.