Destylator przemysłowy to urządzenie, które wykorzystuje proces destylacji do oddzielania różnych substancji na podstawie ich temperatury wrzenia. W przemyśle chemicznym, petrochemicznym oraz spożywczym destylatory odgrywają kluczową rolę w produkcji czystych substancji, takich jak alkohole, oleje eteryczne czy różnego rodzaju chemikalia. Proces ten polega na podgrzewaniu cieczy do momentu, gdy zaczyna parować, a następnie schładzaniu pary, aby skroplić ją z powrotem w postaci cieczy. Dzięki temu można uzyskać substancje o wysokiej czystości, co jest niezwykle istotne w wielu gałęziach przemysłu. W przypadku destylacji frakcyjnej, która jest bardziej zaawansowaną formą tego procesu, możliwe jest oddzielanie kilku składników jednocześnie, co zwiększa efektywność produkcji. Destylatory przemysłowe są stosowane w rafineriach do przetwarzania ropy naftowej, w browarach do produkcji piwa oraz w winiarniach do produkcji win i likierów.
Jakie są rodzaje destylatorów przemysłowych i ich funkcje
W przemyśle istnieje wiele rodzajów destylatorów, które różnią się konstrukcją oraz zastosowaniem. Najpopularniejsze z nich to destylatory prostokątne, kolumnowe oraz wirówkowe. Destylatory prostokątne są najczęściej stosowane w małych zakładach produkcyjnych i laboratoriach. Charakteryzują się prostą budową oraz łatwością obsługi. Z kolei destylatory kolumnowe są bardziej zaawansowane technologicznie i pozwalają na przeprowadzanie skomplikowanych procesów destylacji frakcyjnej. Dzięki swojej konstrukcji umożliwiają one wielokrotne skraplanie pary, co zwiększa wydajność i czystość otrzymywanych produktów. Destylatory wirówkowe natomiast wykorzystują siłę odśrodkową do separacji składników cieczy, co czyni je idealnymi do przetwarzania substancji o dużej gęstości. Każdy z tych typów destylatorów ma swoje unikalne cechy i zastosowania, co pozwala na dostosowanie procesu produkcji do specyficznych potrzeb danego przemysłu.
Jakie są zalety używania destylatorów przemysłowych w produkcji
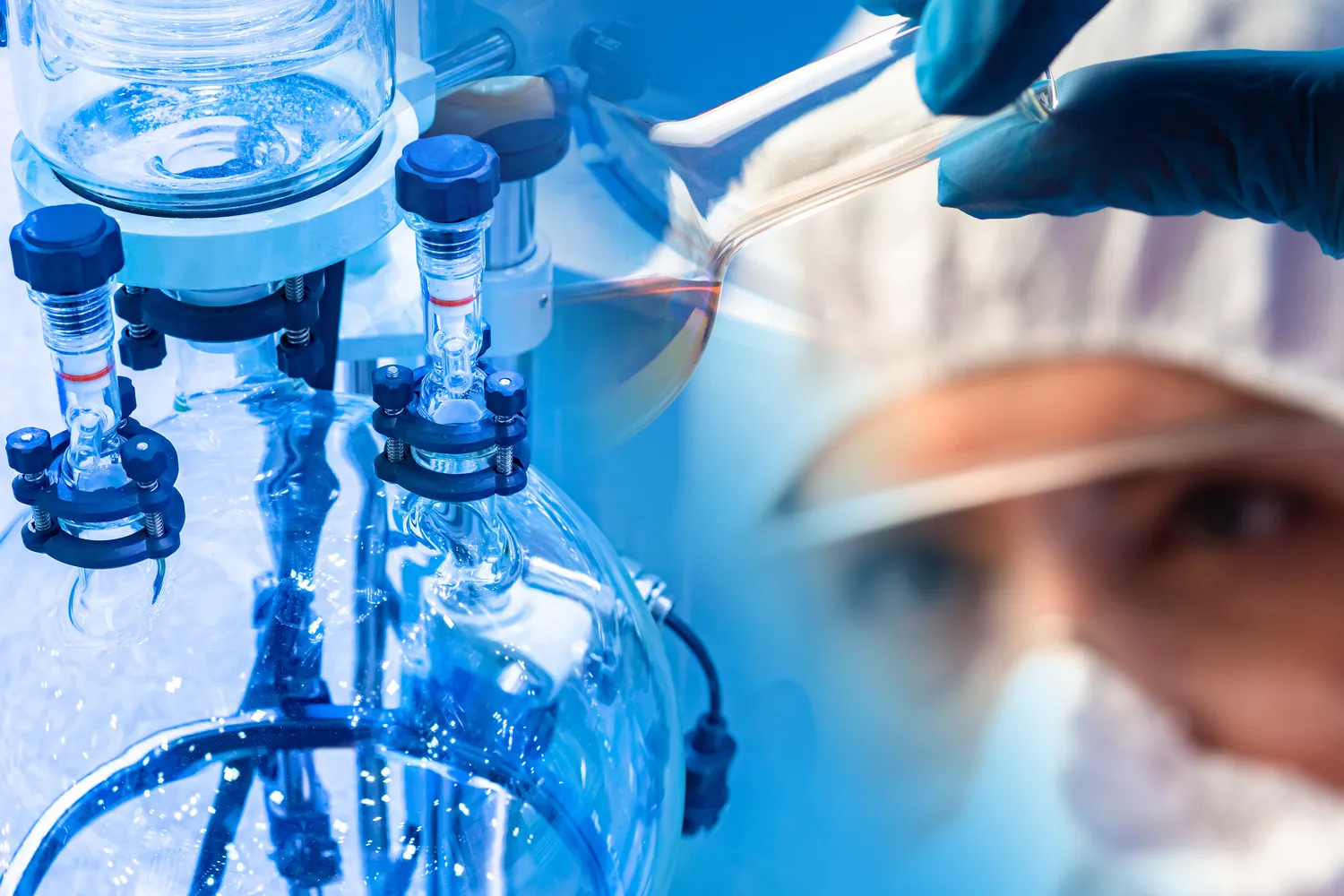
Użycie destylatorów przemysłowych przynosi wiele korzyści dla producentów w różnych branżach. Jedną z głównych zalet jest możliwość uzyskania wysokiej czystości produktów końcowych. Dzięki precyzyjnemu procesowi destylacji można oddzielić niepożądane zanieczyszczenia oraz inne składniki, co wpływa na jakość finalnych wyrobów. Kolejną istotną korzyścią jest efektywność energetyczna tych urządzeń. Nowoczesne destylatory są projektowane tak, aby minimalizować zużycie energii podczas procesu produkcji, co przekłada się na niższe koszty operacyjne. Dodatkowo wiele modeli wyposażonych jest w systemy automatyzacji, które ułatwiają kontrolę nad procesem oraz zwiększają bezpieczeństwo pracy. Destylatory przemysłowe mogą również przyczynić się do zmniejszenia wpływu na środowisko poprzez efektywne zarządzanie odpadami oraz emisjami gazów cieplarnianych.
Jakie są najnowsze technologie w dziedzinie destylacji przemysłowej
W ostatnich latach rozwój technologii związanych z destylacją przemysłową przeszedł znaczną ewolucję. Nowoczesne rozwiązania obejmują zastosowanie inteligentnych systemów monitorowania i zarządzania procesami produkcyjnymi. Dzięki wykorzystaniu sztucznej inteligencji i analizy danych możliwe jest optymalizowanie parametrów pracy destylatorów w czasie rzeczywistym, co prowadzi do zwiększenia wydajności oraz redukcji kosztów operacyjnych. Ponadto coraz częściej stosuje się technologie membranowe oraz ekstrakcyjne jako alternatywy dla tradycyjnej destylacji, co pozwala na uzyskiwanie czystszych produktów przy mniejszym zużyciu energii. Innowacyjne materiały wykorzystywane do budowy kolumn destylacyjnych również przyczyniają się do poprawy efektywności procesów separacyjnych. Wprowadzenie rozwiązań ekologicznych staje się coraz bardziej powszechne – wiele firm inwestuje w technologie umożliwiające recykling ciepła oraz minimalizację odpadów chemicznych powstających podczas produkcji.
Jakie są kluczowe czynniki wpływające na wydajność destylatorów przemysłowych
Wydajność destylatorów przemysłowych jest determinowana przez szereg czynników, które mają istotny wpływ na efektywność procesu separacji. Jednym z najważniejszych elementów jest temperatura, która musi być precyzyjnie kontrolowana, aby zapewnić optymalne warunki dla destylacji. Zbyt wysoka temperatura może prowadzić do niepożądanych reakcji chemicznych, podczas gdy zbyt niska może skutkować niepełnym oddzieleniem składników. Kolejnym istotnym czynnikiem jest ciśnienie, które również wpływa na temperatury wrzenia substancji. Wiele nowoczesnych destylatorów wyposażonych jest w systemy umożliwiające regulację ciśnienia, co pozwala na dostosowanie procesu do specyficznych właściwości przetwarzanych cieczy. Ponadto jakość surowców ma ogromne znaczenie – zanieczyszczenia w surowcu mogą negatywnie wpłynąć na końcowy produkt oraz obniżyć wydajność całego procesu. Odpowiednia konserwacja i regularne przeglądy urządzeń są również kluczowe dla utrzymania wysokiej wydajności destylatorów.
Jakie są wyzwania związane z eksploatacją destylatorów przemysłowych
Eksploatacja destylatorów przemysłowych wiąże się z wieloma wyzwaniami, które mogą wpływać na efektywność produkcji oraz jakość finalnych produktów. Jednym z głównych problemów jest korozja i osady, które mogą gromadzić się wewnątrz urządzeń w wyniku działania wysokich temperatur oraz agresywnych substancji chemicznych. Regularne czyszczenie i konserwacja są niezbędne, aby zapobiec tym problemom i utrzymać odpowiednią wydajność. Innym wyzwaniem jest zarządzanie odpadami powstającymi podczas procesu destylacji. Wiele branż staje przed koniecznością znalezienia ekologicznych rozwiązań, które pozwolą na minimalizację negatywnego wpływu na środowisko. Wprowadzenie systemów recyklingu oraz odzysku ciepła staje się coraz bardziej popularne w celu zmniejszenia ilości generowanych odpadów. Dodatkowo, zmieniające się przepisy dotyczące ochrony środowiska oraz bezpieczeństwa pracy mogą wymuszać na producentach dostosowanie swoich procesów do nowych norm.
Jakie są trendy w projektowaniu nowoczesnych destylatorów przemysłowych
W ostatnich latach zauważalny jest wzrost zainteresowania nowoczesnymi rozwiązaniami w projektowaniu destylatorów przemysłowych. Coraz więcej firm stawia na automatyzację procesów, co pozwala na zwiększenie efektywności produkcji oraz redukcję błędów ludzkich. Systemy monitorowania w czasie rzeczywistym umożliwiają zbieranie danych dotyczących pracy urządzeń, co pozwala na szybką reakcję w przypadku wystąpienia problemów. W projektowaniu nowych destylatorów zwraca się również uwagę na aspekty ekologiczne – wiele firm dąży do ograniczenia zużycia energii oraz emisji gazów cieplarnianych poprzez zastosowanie innowacyjnych technologii, takich jak odzysk ciepła czy wykorzystanie odnawialnych źródeł energii. Ponadto rośnie znaczenie materiałów o wysokiej odporności na korozję i wysokie temperatury, co przekłada się na dłuższą żywotność urządzeń oraz mniejsze koszty eksploatacji.
Jakie są różnice między destylacją prostą a frakcyjną w kontekście przemysłowym
Destylacja prosta i frakcyjna to dwa podstawowe procesy stosowane w przemyśle do separacji składników cieczy, jednak różnią się one zasadniczo pod względem zastosowania i efektywności. Destylacja prosta polega na jednorazowym podgrzewaniu cieczy i skraplaniu pary, co sprawia, że jest to proces stosunkowo prosty i szybki. Jest najczęściej wykorzystywana do oddzielania substancji o znacznej różnicy temperatur wrzenia lub do oczyszczania cieczy o niewielkiej liczbie składników. Z kolei destylacja frakcyjna to bardziej skomplikowany proces, który pozwala na oddzielanie wielu składników jednocześnie dzięki zastosowaniu kolumny frakcyjnej. W tym przypadku para przechodzi przez kolumnę wielokrotnie, co umożliwia lepsze rozdzielenie składników o zbliżonych temperaturach wrzenia. Destylacja frakcyjna jest szczególnie przydatna w przemyśle petrochemicznym oraz chemicznym, gdzie często zachodzi potrzeba uzyskania czystych frakcji różnych substancji chemicznych.
Jakie są zastosowania destylatorów przemysłowych w różnych branżach
Destylatory przemysłowe znajdują szerokie zastosowanie w różnych branżach gospodarki, co czyni je niezwykle wszechstronnymi narzędziami produkcyjnymi. W przemyśle chemicznym służą do produkcji rozpuszczalników, kwasów czy alkoholi o wysokiej czystości. W branży petrochemicznej są kluczowe dla procesu rafinacji ropy naftowej, gdzie umożliwiają uzyskanie różnych frakcji paliwowych oraz olejów bazowych. Również w przemyśle spożywczym destylatory odgrywają istotną rolę – wykorzystywane są do produkcji alkoholi takich jak whisky czy wódka oraz do ekstrakcji olejków eterycznych z roślin. W farmaceutyce natomiast służą do oczyszczania substancji czynnych oraz produkcji leków o wysokiej czystości. Dodatkowo destylatory znajdują zastosowanie w przemyśle kosmetycznym do produkcji perfum i innych kosmetyków zawierających substancje aktywne pochodzenia roślinnego.
Jakie są przyszłe kierunki rozwoju technologii destylacji przemysłowej
Przyszłość technologii destylacji przemysłowej zapowiada się obiecująco dzięki ciągłemu postępowi technologicznemu oraz rosnącym wymaganiom rynku dotyczących efektywności energetycznej i ochrony środowiska. Jednym z głównych kierunków rozwoju jest automatyzacja procesów produkcyjnych, która pozwala na lepszą kontrolę nad parametrami pracy urządzeń oraz zwiększa ich wydajność. Zastosowanie sztucznej inteligencji i uczenia maszynowego umożliwia optymalizację procesów destylacyjnych poprzez analizę danych i prognozowanie wyników produkcji. Ponadto rozwijają się technologie związane z wykorzystaniem odnawialnych źródeł energii oraz systemami odzysku ciepła, co przyczynia się do zmniejszenia kosztów operacyjnych oraz emisji gazów cieplarnianych. Innowacyjne materiały wykorzystywane do budowy kolumn destylacyjnych również mają potencjał do poprawy efektywności procesów separacyjnych poprzez zwiększenie odporności na korozję i wysokie temperatury.